In today’s rapidly evolving industrial landscape, manufacturing standards are becoming more stringent than ever before. Among the plethora of materials employed in the manufacturing sector, plastics play a pivotal role, thanks to their versatile nature. Ensuring that these materials are of the highest quality is paramount to maintaining the integrity and reliability of the products made from them.
One company leading the charge in setting these standards, especially in the plastic manufacturing sector, is CBM Plastics USA. Like many others, they understand the value of quality control in delivering products that stand the test of time. So, what are the best practices in quality control for plastic manufacturing?
The Importance Of Material Selection
Selecting the right type of plastic for a specific application is of utmost importance. It can significantly impact the success or failure of a product. While it may seem that all plastics are the same, the reality is that raw materials can vary greatly in their molecular structure, strength, flexibility, and heat resistance.
By carefully considering and choosing a superior grade or a more suitable type of plastic, manufacturers can enhance their products’ durability, functionality, and safety. This ensures that the end product meets the desired requirements and performs optimally in its intended application.
Regular Inspection And Monitoring
Performing routine checks and monitoring is crucial to maintaining smooth operations of production lines. However, going beyond a surface-level examination of the finished product is important. It involves delving deep into the manufacturing process. This includes monitoring and controlling factors such as the temperatures at which the plastics are molded, the speed of the production line, and even the humidity levels in the manufacturing environment.
By conducting regular inspections, faults and issues can be identified and rectified before they have the chance to impact the final product. This vigilance ensures that every product coming off the production line is consistent and meets the required quality standards. Regular inspections and monitoring are key in delivering a reliable and consistent output, preventing inconsistencies and defects from reaching the customers.
Training And Skill Development
The success of a production line heavily relies on the knowledge and expertise of the people operating it. Therefore, investing in training programs is essential to ensure the team is equipped with the latest techniques and best practices in plastic manufacturing. By providing regular training sessions, manufacturers can keep their team members up-to-date and enable them to identify potential issues before they escalate.
Additionally, a well-trained team can optimize production processes to improve efficiency and maintain high-quality standards. Training and skill development empower employees to perform at their best and contribute to the overall success and competitiveness of the manufacturing company.
Adopting Advanced Technology
Incorporating new technologies can have a significant impact on enhancing manufacturing processes. Manufacturers can enjoy precise control over the production line by embracing computerized systems and automation. For example, real-time monitoring systems can detect and flag deviations from the standard process, allowing immediate adjustments. This level of automated control removes the possibility of human error. It ensures that tasks are carried out to the highest quality standards.
Additionally, technology can simplify complex manufacturing processes and reduce production time. Keeping up with modern technological advancements can improve manufacturing efficiency, product quality, and overall customer satisfaction, providing a competitive edge in the market.
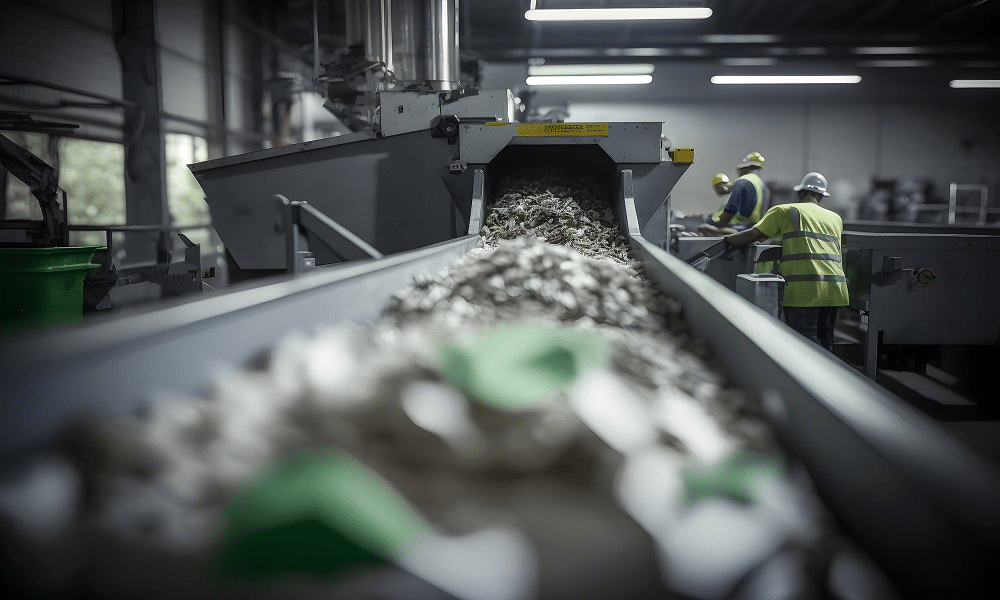
Feedback Loops And Continuous Improvement
A robust feedback system is essential for manufacturers to continuously improve their products and processes. Feedback can come from various sources, such as customer feedback, input from distributors, or feedback from internal teams. This feedback is invaluable as it provides valuable insights into areas that need improvement and helps identify potential issues or customer concerns.
By actively listening and incorporating this feedback into the manufacturing process, manufacturers can ensure that quality remains a top priority. Continuous improvement is achieved using feedback to make necessary adjustments, implement changes, and refine operations to meet and exceed customer expectations. This iterative approach empowers manufacturers to consistently enhance their products, processes, and overall performance, increasing customer satisfaction and business success.
Ensuring Compliance With Industry Standards
In plastic manufacturing, adherence to industry standards and regulations is crucial to guarantee product safety, durability, and environmental sustainability. These standards define the quality benchmarks manufacturers must meet to maintain the highest product integrity. Staying informed about the latest standards relevant to the industry is essential. Ongoing education and awareness regarding these standards enable manufacturers to understand the requirements and take proactive measures to comply with them.
Regularly auditing manufacturing processes is another vital aspect of ensuring compliance. Audits help identify gaps or areas of non-compliance, allowing manufacturers to make necessary adjustments to meet the standards.
Maintaining A Clean And Organized Production Floor
A clean and organized production floor plays a vital role in ensuring plastic products’ high quality and integrity. Surprisingly, even small amounts of dust, debris, or moisture can significantly impact product quality. Regular cleaning and maintenance of the production environment reduce the risk of foreign contaminants compromising the product during manufacturing. It is crucial to establish robust cleaning protocols and schedules to remove any potential sources of contamination. Additionally, organizing the production floor facilitates efficient movement, minimizes the chances of errors or accidents, and promotes a safer working environment.
The Role Of Testing And Verification
Testing and verification are crucial in ensuring product quality and safety. Rigorous testing of products before they hit the market is imperative to identify and address any potential issues. Testing covers various aspects such as stress testing, heat resistance, chemical resistance, and durability, amongst others. The aim is to ensure that the product meets real-world conditions and performs as expected in the hands of consumers.
By performing these tests, manufacturers can identify and address any potential product defects before the product reaches the market. Verification and testing also help instill confidence in customers about the quality and safety of the product, which is a crucial factor in building customer trust and product reputation and ultimately driving business success.
The Bigger Picture: Protecting Brand Reputation
Brand reputation is a critical factor in the success of any business. In the plastic manufacturing industry, it hinges on the quality of products. The mere presence of a faulty batch or lower-quality products in the market can significantly damage a brand’s image and reputation. Given the high competition in the market and the ease with which information spreads in today’s world, even a single negative experience can have a lasting impact.
Hence, it is crucial to prioritize quality control measures and adopt best practices in plastic manufacturing to ensure brand protection. Strict adherence to quality control measures, thorough testing and verification, and consistent implementation of industry standards and regulations all contribute to building and maintaining a positive brand reputation.
Conclusion
Quality control in plastic manufacturing isn’t just about adhering to industry standards. It’s about understanding the nuances of the material, refining the process continuously, and ensuring that every product is a testament to your brand’s commitment to excellence. Adopting these best practices safeguards your brand’s reputation and instills customer trust. Pursuing quality is an ongoing journey that every manufacturer must embark upon with dedication and diligence.
The post Quality Control In Plastic Manufacturing: Best Practices appeared first on Tweak Your Biz.
0 Commentaires